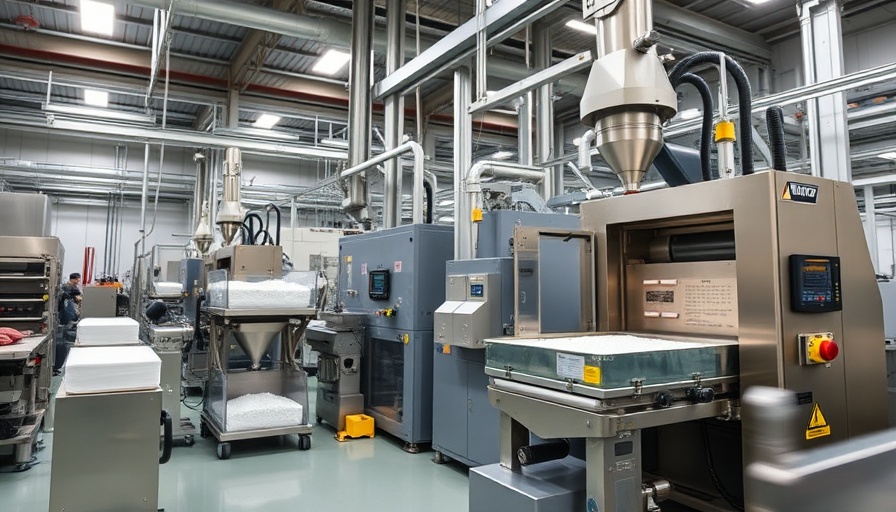
Revolutionizing Battery Production: The Laser Drying Breakthrough
In the quest for more efficient battery production, a significant advancement has been made in laser-based drying techniques. The recent conclusion of the IDEEL project in Germany represents three years of intensive collaboration among scholars and industry experts, aimed at enhancing the manufacturing process of lithium-ion battery components. Researchers at RWTH Aachen University, along with prominent partners, have developed a sophisticated laser drying process that not only accelerates production speed but also enhances energy efficiency.
The Importance of Efficient Drying in Battery Production
Manufacturing lithium-ion batteries, essential for electric vehicles and renewable energy storage, traditionally involves slow and energy-intensive drying methods. As highlighted by Professor Achim Kampker, director of the Production Engineering of E-Mobility Components (PEM) at RWTH Aachen, the roll-to-roll electrode drying process has long been a major contributor to energy consumption and production costs. The conventional practice necessitated the use of massive gas-fired furnaces, often positioned in energy-draining clean rooms.
The Laser-Based Solution: Speed and Sustainability
The newly developed hybrid drying process marks a turning point for battery manufacturing. By first employing high-power diode lasers for predrying, before transferring to a smaller oven for finishing touches, manufacturers can achieve a web speed of 30 meters per minute. The innovation not only halves the necessary furnace length but also promises operational cost reductions of 20 to 30 percent. Importantly, this advancement reflects a movement towards more sustainable and climate-friendly production methods in battery technology, crucial for a greener future in transportation and energy.
Compatibility and Quality: A Step Towards Industrial Integration
During the IDEEL project, researchers formulated new anode and cathode coatings using a combination of graphite, lithium iron phosphate, and silicon graphite. Achim Kampker emphasizes that despite the rapid production capabilities, the new drying process maintains high standards, ensuring that adhesion, residual moisture, and electrical conductivity remain at optimal levels.
The Future of Battery Production: Integration and Scalability
The next phase of this innovation will see the laser drying process integrated into the working practices of the Fraunhofer FFB in Münster, demonstrating the project's readiness for industrial application. With appropriate scaling and attention to detail, experts believe that the increased throughput rates will not only sustain quality but will also expedite the overall production timelines for lithium-ion batteries.
Global Relevance and Industry Impact
The implications of these advancements are far-reaching, especially given the burgeoning demand for electric vehicles and renewable energy solutions. As home and business owners increasingly turn to solar-powered solutions and electric transportation, innovations in battery technology become paramount. The ability to produce batteries more efficiently and sustainably will directly impact the affordability and accessibility of green technologies.
Call to Action: Embrace the Future of Energy
As the trends toward sustainability gain momentum, it is essential for both homeowners and businesses to stay informed about developments in energy production technologies. The nuanced understanding of battery manufacturing processes not only highlights the changing landscape of energy consumption but also paves the way for smart investments in solar and electric energy solutions. Consider exploring how these innovations can be leveraged in your own financial and energy planning.
Write A Comment